Manufacturing Industries Can Be Fun For Anyones
Wiki Article
10 Easy Facts About Oem Described
Table of ContentsThe 20-Second Trick For MfgWhat Does Die Casting Mean?A Biased View of Lean ManufacturingThe Of Lean Production
With shot moulding, pre-dried granular plastic is fed by a forced ram from a receptacle into a heated barrel. As the granules are gradually relocated onward by a screw-type plunger, the plastic is pushed into a warmed chamber, where it is thawed. As the plunger advances, the thawed plastic is forced through a nozzle that relaxes against the mould, allowing it to get in the mould tooth cavity through an entrance and runner system.Shot moulding cycle [modify] The series of events throughout the shot mould of a plastic component is called the injection moulding cycle. The cycle starts when the mould shuts, adhered to by the shot of the polymer right into the mould cavity. When the tooth cavity is loaded, a holding stress is kept to make up for product contraction.

Once the tooth cavity is 98% complete, the machine switches from rate control to stress control, where the tooth cavity is "packed out" at a constant pressure, where enough rate to reach preferred pressures is required. This lets employees manage part dimensions to within thousandths of an inch or better. Various kinds of shot moulding processes [edit] Although most injection moulding procedures are covered by the traditional process summary above, there are several important moulding variations including, yet not limited to: A more thorough listing of injection moulding procedures might be discovered here: Process repairing [ edit] Like all industrial processes, injection molding can generate problematic components, even in toys.
Plastic Manufacturing Can Be Fun For Everyone
Trials are commonly performed before complete production runs in an effort to predict issues and figure out the ideal requirements to make use of in the shot process.: 180 When loading a new or strange mould for the very first time, where shot size for that mould is unknown, a technician/tool setter might carry out a dry run before a complete production run.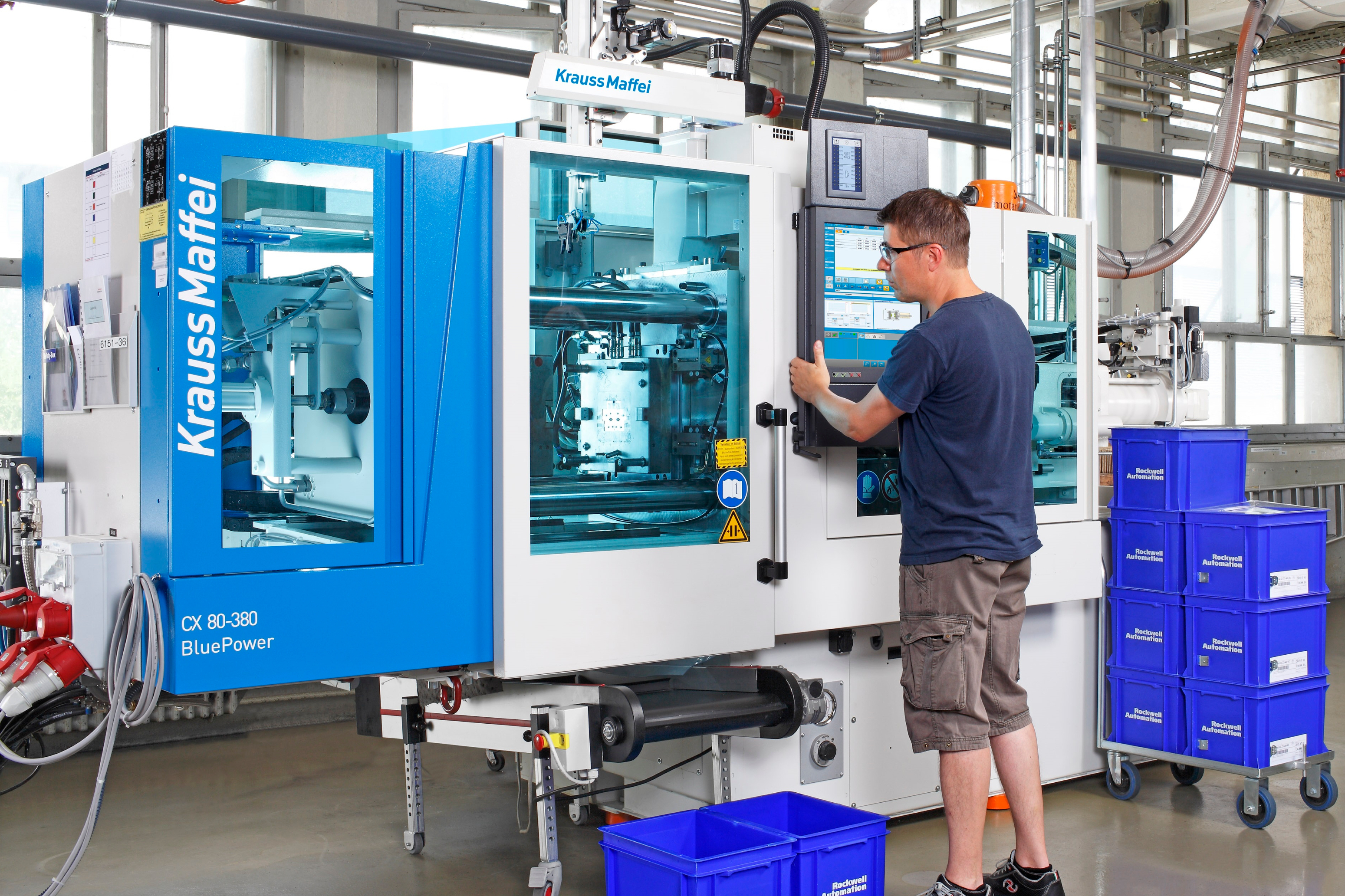
Holding pressure is raised until the parts are without sinks and part weight has been attained. Molding problems [modify] Shot moulding is an intricate technology with possible production issues. They can be triggered either by problems in the moulds, or more frequently by the moulding procedure itself.: 4785 Moulding problems Different name Descriptions Triggers Blister Blistering Elevated or layered area on surface area of the part Device or material is too warm, frequently triggered by a lack of cooling around the device or a defective heating system.
About Plastic Manufacturing
Embedded particulates International particle (scorched product or various other) ingrained in the part Particles on the device surface area, polluted material or international particles in the barrel, or as well much shear warmth shedding the product prior to injection. Circulation lines Directionally "off tone" wavy my response lines or patterns Injection speeds too sluggish (the plastic has actually cooled down excessive during injection, injection speeds should be set as quick as is ideal for the procedure as well as product used).Loading also quickly, not enabling the edges of the component to establish. Additionally mould might be out of registration (when both halves do not centre properly and component walls are not the exact same density). The supplied information is the common understanding, Improvement: The Absence of pack (not holding) stress (pack pressure is made use of to load out despite the fact that is the component throughout the holding time).
Simply put, as the part reduces the resin divided from itself as there was not adequate resin in the tooth cavity. The void could take place at any kind of area or the part is not limited by the thickness but by the material flow and also thermal conductivity, yet it is more probable to take place at thicker locations like ribs or managers.
Knit line/ Blend line/ Transfer line Discoloured line where 2 circulation fronts fulfill Mould or worldly temperatures set too low (the product is cold when they fulfill, so they don't bond). Time for change in between injection and transfer (to packing and also holding) is prematurely. Twisting Altered component Air conditioning is also short, product is as well warm, lack of cooling around the device, wrong water temperatures (the components bow inwards in the direction of the hot side of the tool) Irregular shrinking between locations of the component.
Some Ideas on Manufacturing You Should Know
125 inch wall surface density is +/- 0. 008 inch (0. 2 mm).: 446 Power requirements [edit] The samsung foundry power needed for this process of injection moulding depends upon lots of things and ranges products made use of. Manufacturing Processes Recommendation Overview states that the power requirements rely on "a product's specific gravity, melting point, thermal conductivity, component size, and molding rate." Below is a table from page 243 of the exact same recommendation as formerly mentioned that ideal highlights the attributes appropriate to the power required for the most commonly utilized products.Along with mounting inspection systems on automated gadgets, multiple-axis robots can remove parts from the mould and also place them for more procedures. Certain instances consist of eliminating of parts from the mould instantly after the components are created, in addition to applying device vision systems. A robotic holds the component after the ejector pins have been prolonged to release the part from the mould.
Why is shot molding device manufacturing so reliable? What is Shot Molding?
The injection molding equipment uses tailor-made molds to load them out according to requirements, producing similar copies that can be tailored in a variety of means. What's more, shot molding is a really versatile procedure, enabling for a broad variety of different materials and finishes, that makes it a popular choice in many sectors with totally various objectives as well as demands - oem.
Report this wiki page